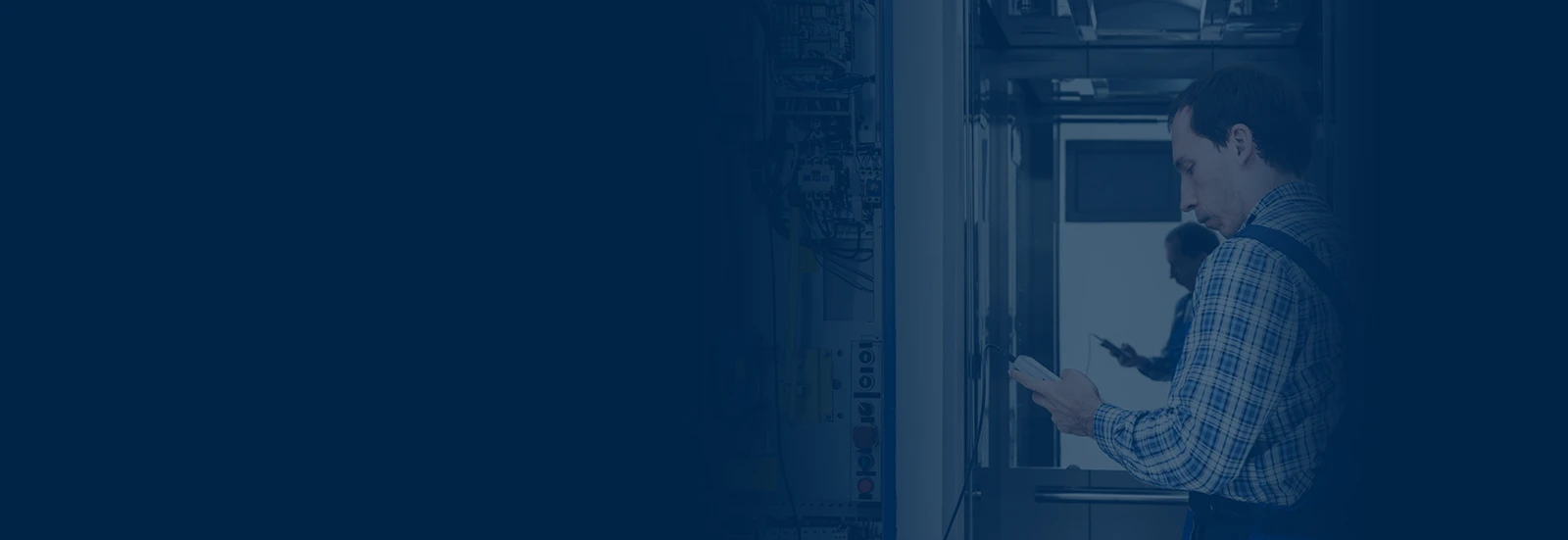
Use Case
Kickstart asset modernization with guided inspection workflows
Adaptive feasibility surveys improve productivity and revenue recognition for elevator company
A global elevator manufacturer wanted to embark on a modernization initiative by updating its deployed assets to the latest generation connected elevators. At the time, less than 50% of elevators in service were current.
In order to take stock of its existing equipment and which of them can be reasonably replaced, the manufacturer needed to perform feasibility surveys. These surveys were to account for the age and updatability of field assets, the results of which would allow the business make decisions on whether to update, replace, or keep the equipment.
CHALLENGES
Low asset visibility
Existing data on deployed assets do not include the level of detail required to make informed decisions. The organization wanted a deeper understanding of its existing elevators and needed a streamlined way to perform asset inspections.
Unsuitable software for the field
Equipment surveys were conducted using spreadsheets, making the process tedious for mobile users. The current software was not designed for field work.
Excessive technician travel
Because there was little visibility into asset information, technicians were needing to come on site multiple times to perform thorough inspections.
SOLUTION
TrueContext designed a guided contextual survey, directing field technicians on which data points to capture and which measurements to take on the job. The survey delivered resource images to enable users to competently perform the inspections, regardless of experience or skill level.
The workflow adapted based on the specific asset being surveyed so that technicians could capture the information required for the business to assess feasibility. Only potential candidates were tagged for a full technical inspection based on survey findings.
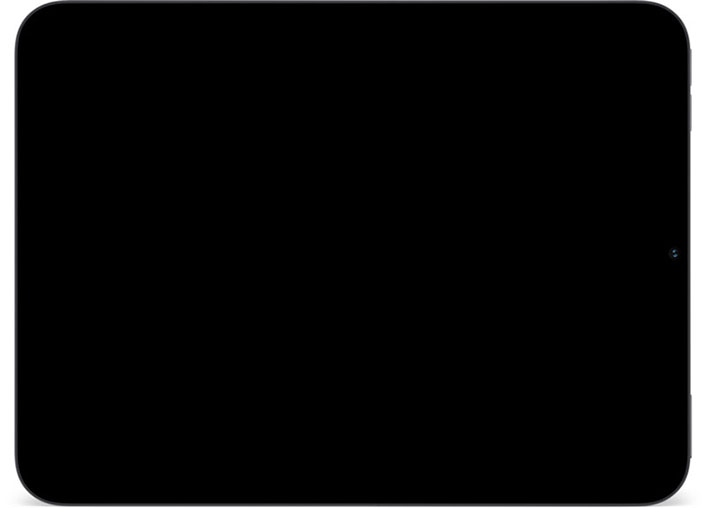
OUTCOMES
Improved data quality
The workflows adapted to the specific asset being inspected, so only relevant data would be captured. Information would be validated on the spot based on acceptable ranges.
Accelerated revenue recognition
When assets were tagged for update, full technical inspections were scheduled and completed, with a quote immediately sent to the customer for approval.
More efficient inspections
The surveys enabled technicians to move quickly through the workflow with an intuitive mobile app as a primary data capture tool.
Increased worker safety
Safety and compliance were woven into the survey workflows, ensuring protocol be followed by technicians performing the work.
Reduced technician travel
Only candidates for upgrade would require a more robust technical inspection, so technicians only return to site to perform the work when necessary.
Streamline elevator inspections with TrueContext
Book a 15-minute chat to learn how you can make TrueContext work for you.